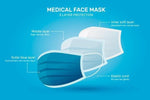
Difference between Melt blown and Spun bonded filters
, 2 min reading time
, 2 min reading time
Traditionally, Spun bonded filters have been used widely in face mask manufacturing as they are the cheaper more readily available however there is a difference between the two filters due to the manufacturing processes.
Melt blown filters are made by laying fine continuous polymer fibres and blowing out the fibres by applying heat directly on the fibres creating a self-bonded web. These fibres tend to be 15-35 micrometre in diameter. Unfortunately, this process limits the type of polymer fibres that can be used resulting in higher costs in comparison to spun bonded filters all though higher consistent results are achieved.
Spun bonded
Typically spun bonded techniques use thermoplastic polymers, which have high molecular weight and broad molecular properties, fed to a spinneret. The fibres are then spun into position and a typically bonded by using techniques such as solvents, electricity etc. Due to the techniques and fibres used, the filters are thicker when compared to the melt blown filters. As this technique is not restrictive to a type of fibre the cost of manufacturing is often cheaper, however, results can vary based on the type fibres used and the adhesion processes employed
Due to the lower quality, the spun bonded filters require additional layers compared to the melt blown to ensure comparable results. The spun bonded fibres are highly absorbent being highly beneficial in wound management whereas the melt blown filters have excellent barrier properties.
It has been clinically evidenced that melt blown filters can produce higher results based on the ASTM standards with just one layer of melt blown against one layer of spun bonded. According to the Nelson reports from 2017, a melt blown filter of greater than 25g thickness produces a result of >98% BFE and fluid filtration of 160 mm/hg. It is interesting to note that other clinical reports have shown melt blown filters that report a BFE of >95% still producing a fluid filtration of 160mm/hg. Unfortunately, spun bonded filters require multiple additional layers and increase thickness in order to produce results that are compliant to the ASTM standards. This is often why it can be deceiving when comparing the two types of masks. Spun bonded masks are thicker due to the number of layers required to provide sufficient protection whereas the melt blown are thinner while still producing high level results. Sight evaluation can be deceiving when it comes to mask quality.
Unfortunately, when comparing a mask that uses a melt blown filter to a one that uses spun bonded filter, thickness is not a valid method of evaluating comparable effectiveness. Caution should always be had with spun bonded to ensure consistent results due to potential fibre variations that can negatively affect compliance to the standards. With melt blown filters stability and consistency is increased and compliance to standards can be achieved with fewer, thinner layers.